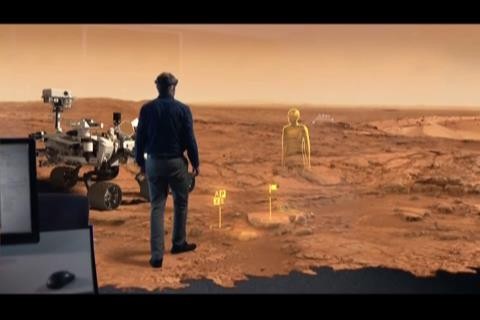
Validating all designs in “Virtual World” using CAD Models or “Virtual Twins” is one of the pillars of Industry 4.0
For instance, if you are into designing a process for machining a part you have CAD models of machine, fixture, part that you wish to make, cutter and cutter path to verify and forecast any fouling / crash, cycle time, quality of part made, chatter marks, energy consumption, cutter life, productivity, operating cost and so on. Only when you are reasonably sure of outcome you invest further in the real world acquisitions.
There is vast variability in domain, depth and level of Software Simulation:
For Engineering aspects:
- Only 3D CAD models are used primarily for visualization, exploded views, virtual assembly / dismantling and dimensional measurements.
- Above could be with animated movements and detection of fouling / collision
- Solid models are used with impressed kinematic, static and dynamic forces and heat maps are generated for stress, strain, deflection, vibration
- It could be with heat flow, temperature mapping and Computational Fluid Dynamics
- Simulation of Machining and Assembly Cycle time and ergonomics
- Simulation of sheet forming and defects
- Simulation of processes for casting, forging, welding and heat treatment showing stresses, cooling pattern, distortions and metallurgical phase distribution / microstructure, surface hardness and strength
- Simulation of Shop Floor Layouts, Movements, Equipment Installation Project and with complete process flow
It could be much simpler dynamic excel-sheet based prediction on management aspects using simple math:
- Work Flow: Tracking of schedules, Tracking of projected and instantaneous delivery and
- Simulation of cost for a Work Order
- Simulation of Production shop Performance such as OEE, Inventory, Productivity and Efficiency.
- Simulation of Mudas – Loss Mapping & Consumptions
- Simulation of Logistics, Warehousing and Supply Chain
- Simulation with associated Cost of Materials, Conversion and Overheads
- Simulation of Market Conditions and Changing demands
- Simulation of Cash flow / funds
- Simulation of Business and Business Performance
BUT, Simulations have been around for over two decades …what is the difference between “Processing for Virtual World” as Simulation?
- Well, the only difference is “depth” and “end to end integration”.
- Usually Simulations use a limited FE Analysis for certain isolated domain of physics e.g., elasticity / solid modelling / heat flow / vibration / mechanics.
- In sheet formability simulation it assumes:
o Homogeneous properties of sheet
o Ideal theoretical surface of Dies
o Ideal movements and forces
o Thinning / wrinkling or cracks are predicted largely based on stress-strain and material flow ….
If it also considered thermal expansion, deflection, play and vibrations of Dies and Press also it would be closer to “Virtual Twin”
Simulation in isolation tends to be like “techno astrology” where predictions are made without considering probable effect of Rahu-Ketu and Shani
AVINASH KHARE