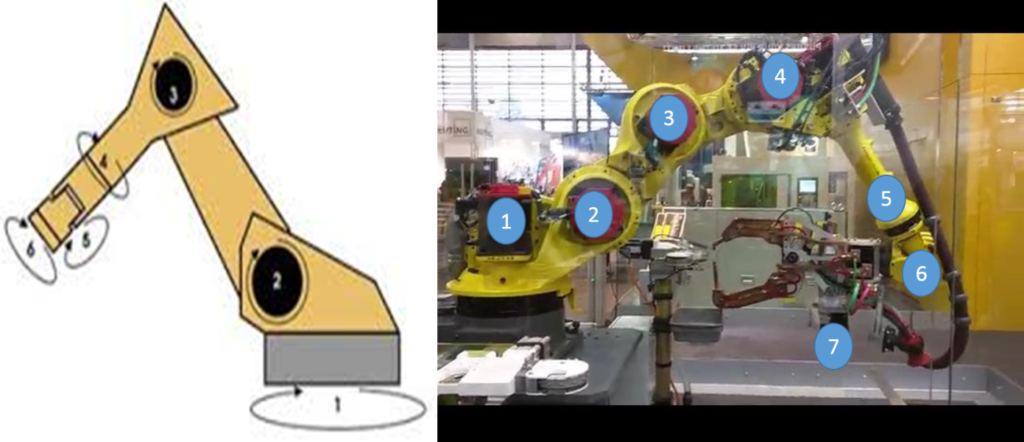
Buying and putting “Standard Articulating Arm Robot” to applications of material handling automation is in vogue these days, usually resulting in job cuts for manpower. While Industry 4.0 has included Robotic Automation as one of the pillar; Industry 5.0 acknowledges the superiority of human flexibility, adaptability and dexterity over automation with standard Robots.
Let us objectively evaluate where Robots fall short:
1. Limited Dexterity and Reach within work envelope:
a. Standard 6 axes Robots have linkages and motorized nodes whereby only the angle of linkages could be changed. The fixed length of linkages result into exclusion zones where Robot cannot reach … just as you are unable to scratch much of your arm ( away from shoulder ) with fingers of same hand.
b. As shown in right side of picture, it may be possible to break the linkages by putting additional node for overcoming this limitation, partly.
c. But how many controlled movements could you have in a Robot as compared to human hand with 17 nodes
d. What nature and Robot Manufacturers have not done so far is to replace fixed length linkages with variable length linkages ( such as hydraulic cylinders or telescopic boom of cranes ) ; where angles as well as length of linkages could be changed for faster and extending reach into exclusion zones.
2. Adaptive Automation is difficult:
a. Robots follow the programmed trajectory and follows commands to end effector blindly e.g., it will make a welding run without seeing deviations in seam to be welded and regardless of the quality of weld. While Robot can do wire fed TIG / MIG welding BUT have you ever seen a Robot doing Arc Welding with fixed length electrodes like human welder? NO … it cannot adaptively feed the electrode as it gets consumed.
b. Similarly if it is painting it cannot make sure that paint reaches uniformly in crevices
c. You can program Robot to pick cold drink bottles vertically from crate and keep them on conveyor provided crate is kept at same place in same way within certain accuracy …BUT it cannot pickup cold drink bottles from a bucket unless it has a vision system and flexible intelligence to orient itself according to orientation of bottle at the top … it has been done experimentally but it is not so common and affordable in practice.
d. With vision system and force sensor augmentation it is possible to have adaptive where Robot could jiggle bolts to gently align them through mismatched bores by hit and trial before pushing it hard … BUT it is not so common and affordable … human operative would anytime be more affordable and desirable.
3. Robot cannot apply set force perpendicular to a surface and it cannot adaptively maintain a fixed gap /ride-on standoff from the surface :
Robot works in position control mode and it applies force as required to reach commanded position within its torque limit at nodes … it tries to reach commanded position at all times BUT Robot cannot do something like hand filing , polishing or grinding a job in multiple passes in force control mode.
While Robots can blindly execute the programmed trajectory repeat ably therefore the process they are entrusted must have certain accuracy just for the sake of Robotic automation. Robots cannot be entrusted jobs which require adaptive working to adjust against variability which is so common in practical situations.
AVINASH KHARE