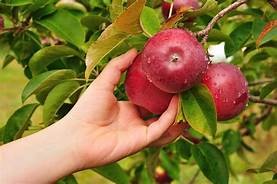
Now a days everybody in Manufacturing Equipment and Automation parlance is chasing Industry 4.0 since it seems to be vital evolution for “future compatibility” and as for any other popular industrial best practice; esteemed manufacturing organizations would like to have some “Certificate of Compliance” for flaunting as well as for self-assurance.
- BUT then, Industry 4.0 is not quite like an ISO standard or Business Excellence Model that could be simply audited / assessed against clauses specified in a manual for Certification or Scoring.
- It is loosely the use of all or few of the nine technologies involving Data Automation in manufacturing , that entitles an organization to have implemented Industry 4.0
- Since full blown Industry 4.0 implementation looks formidable in terms of investment and adoption of hi tech; Indian industry generally seeks to start with some “Baby Steps” OR “Low Hanging Fruits” to convince itself for its commercial viability.
What are usually the Low Hanging Fruits?
1. OEE
2. Condition Based Predictive Maintenance
3. Energy Consumption Monitoring
4. Productivity Dashboard
5. Production Schedules
6. Andon Boards with automated Dash-boarding
7. Use of Cobots
8. Use of Simulations
9. Use of Virtual Reality for Training and Image processing for Inspection / Surveillance
10. Use of Smartphone based apps
What do Low Hanging Fruits fail to kick start Industry 4.0 in bigger way?
- Most of these could be “safely” done without rocking the boat or exposing skeletons in the cupboard.
- Most of these are standard features being supplied by equipment builders and software sellers and they are expected to be “plug and play”
- Most of them get implemented “piecemeal” in isolation
- Often they do not have a convincing tangible benefits and ROI
- Most of these were being done well before Industry 4.0 was born; where organizations found them worth implementing … I4.0 has only perhaps made them easier to do with automation
Often the “Best Practices” may not be relevant today and the way they get implemented in sweeping manner may be counterproductive…e.g.,
- When management insists on doing OEE for all machines they fail to realize that it makes sense only for the “bottleneck” machine
- What is the use of achieving 90% OEE if the Businesses are currently operating well below their installed capacity?
Where are we missing the point?
- Before we get data we must be clear what we will do with that data in terms of generating actionable intelligence beyond just splashing dashboards and reports.
- How are we going to take corrective / improvement actions based on data through Predictive and Adaptive route? While contemplating Industry 4.0 we have to be clear about the entire “control loop” and … How it would work?
- Industry 4.0 has more to do with the “Grand Integration” and “connecting shop floor to top floor” but we find that integration with ERPs is seldom being contemplated.
- Piecemeal implementation defeats the very idea of grand integration.
If we feel our organizations have lot of scope for improvement that possibly we are not able to see today …we can be rest assured that full blown Industry 4.0 with “Grand Integration” will certainly throw up possibilities for substantial tangible benefits…. just as advent of Smartphones have totally transformed the way we transact today … which nobody anticipated before it actually happened, with whole ecosystem and practices developing around that technology.
Avinash Khare